3D printing has taken the manufacturing world by storm, transforming ideas into tangible objects with the simple click of a button. This incredible technology, also known as additive manufacturing, builds objects layer by layer, offering a versatile and efficient alternative to traditional manufacturing methods. Let’s explore the various types of 3D printing technologies, each with unique processes, applications, and the magic they bring.
Stereolithography (SLA): Precision and Detail
Imagine creating intricate architectural models, detailed prototypes, or even artistic toys with smooth surfaces and fine details. That’s the power of Stereolithography (SLA), one of the oldest yet most precise 3D printing technologies.
How It Works: SLA uses a UV laser to cure liquid photopolymer resin into solid plastic, layer by layer. The laser draws the design onto the surface of the liquid resin, hardening it as it moves along.
Applications: SLA shines in industries where precision is critical. Architects use it to create detailed scale models of buildings, manufacturers produce complex prototypes for testing, and artists craft unique toys and collectibles. Additionally, SLA is popular in the dental and medical fields for creating accurate models and tools.
Why It’s Fascinating: The level of detail SLA can achieve is astonishing. If you’ve ever held a perfectly smooth, intricately designed model in your hand, there’s a good chance it was made using SLA. This technology’s ability to bring complex designs to life with such precision is what makes it so beloved.
Fused Deposition Modeling (FDM): The People’s 3D Printer
A 3D printer in a classroom, a hobbyist’s workshop, or a small business is probably using Fused Deposition Modeling (FDM). This is the most common and accessible 3D printing technology, known for its simplicity and versatility.
How It Works: FDM printers heat and extrude thermoplastic filament through a nozzle, which deposits the material layer by layer to build up the object. The beauty of FDM lies in its straightforward process, which makes it easy to use and affordable.
Applications: FDM is incredibly versatile. It’s used for everything from creating prototypes and simple tools to producing low-cost parts and educational models. The wide range of materials, including ABS, PLA, and PETG, allows for producing objects with varying degrees of strength, flexibility, and durability.
Why It’s Fascinating: FDM democratizes 3D printing. It’s the technology that brings 3D printing into homes, schools, and small businesses, allowing anyone with an idea to bring it to life. Its affordability and ease of use make it the go-to choice for many.
Selective Laser Sintering (SLS): Power and Performance
Selective Laser Sintering (SLS) is the answer when strength and durability are required. This technology is a powerhouse capable of producing tough, functional parts without additional support structures.
How It Works: SLS uses a high-powered laser to fuse small particles of powdered material, typically nylon, into a solid object. The laser scans the powder bed, sintering the material together, layer by layer, to create the desired shape.
Applications: SLS is widely used in industries that require robust, functional parts, such as aerospace, automotive, and consumer goods. From creating lightweight components for airplanes to durable gears and brackets, SLS is the go-to technology for parts that must withstand real-world use rigours.
Why It’s Fascinating: SLS’s ability to produce strong, complex parts without additional support is impressive. The technology opens up possibilities for designs that would be impossible or prohibitively expensive to manufacture using traditional methods.
PolyJet: A Symphony of Materials and Colors
PolyJet is the artist of the 3D printing world, capable of producing parts with intricate details, smooth surfaces, and various materials and colors—all in a single print. It’s like having a painter’s palette at your disposal, but you’re working with high-tech polymers instead of paint.
How It Works: PolyJet technology jets layers of liquid photopolymer onto a build tray, which is then instantly cured by UV light. What makes PolyJet unique is its ability to blend different resins during the printing process, allowing for the creation of multi-material and multi-color parts.
Applications: This technology is a favorite in industries where appearance and texture matter. It’s used to create lifelike medical models, detailed prototypes for consumer products, and any application where the visual and tactile quality of the part is crucial.
Why It’s Fascinating: PolyJet’s versatility is mind-blowing. The ability to print parts with varying material properties in a single process and in full color opens up a world of possibilities for designers and engineers. Whether you’re creating a realistic anatomical model or a multi-colored prototype, PolyJet delivers stunning results.
Direct Metal Laser Sintering (DMLS): Metal Mastery
When it comes to printing metal parts with intricate designs and superior strength, Direct Metal Laser Sintering (DMLS) is the star. This technology redefines what’s possible in industries that rely on high-performance metal components.
How It Works: DMLS works similarly to SLS but with metal powder. A laser selectively fuses the powdered metal, layer by layer, to create a solid object. The result is a fully dense metal part ready for demanding applications.
Applications: DMLS is used in industries such as aerospace, medical, and automotive, where the ability to produce complex metal parts quickly and accurately is a game-changer. From custom orthopedic implants to lightweight aerospace components, DMLS is pushing the boundaries of what metal manufacturing can achieve.
Why It’s Fascinating: The fact that you can print a fully functional metal part with intricate geometries that would be impossible to machine is nothing short of revolutionary. DMLS is enabling innovations in fields where performance and precision are critical.
Multi Jet Fusion (MJF): Speed and Precision
Multi Jet Fusion (MJF) technology is known for its speed and precision, making it a top choice for producing high-quality parts quickly. It’s like the sports car of 3D printing—fast, efficient, and high-performing.
How It Works: MJF uses fine-grained powder, typically nylon, that is spread across the build platform. An array of inkjet nozzles applies fusing and detailing agents, and then infrared light passes over the surface to fuse the powder into a solid layer.
Applications: MJF is used in industries that require fast turnaround times and high-quality parts, such as consumer electronics, automotive, and medical devices. Whether you need functional prototypes or small production runs, MJF delivers quickly and accurately.
Why It’s Fascinating: MJF combines speed and precision in a way few other technologies can. It’s perfect for situations where time is of the essence without compromising on the quality of the final product.
Binder Jetting: Versatility and Volume
Binder Jetting is a versatile additive manufacturing technology that can handle various materials, including metals, ceramics, and sand. It’s particularly well-suited for producing large volumes of parts quickly and efficiently.
How It Works: In binder jetting, a liquid binder is selectively deposited onto a powder bed, binding the particles together. This process is repeated layer by layer until the part is complete. After printing, the part is typically sintered in a furnace to enhance its mechanical properties.
Applications: Binder Jetting is used in industries such as casting, which can produce sand molds, and manufacturing, where it can create metal parts in large quantities. It’s also capable of producing full-color prototypes and even artistic pieces.
Why It’s Fascinating: The ability to print large quantities of parts quickly, with a variety of materials, makes Binder Jetting a versatile tool in the 3D printing arsenal. It’s perfect for applications where both volume and versatility are required.
Conclusion: The Future is Now
3D printing is no longer just a futuristic concept—it’s here, and it’s transforming industries across the globe. From the intricate detail of SLA to the robust strength of DMLS, each 3D printing technology offers unique advantages that cater to different needs. Whether you’re an architect, an engineer, a medical professional, or just someone with a creative idea, there’s a 3D printing solution for you.
As 3D printing technologies evolve, we can only imagine the incredible innovations that lie ahead. Stay curious, stay creative, and explore the endless possibilities that 3D printing has to offer.
For more insights and to explore 3D printing services, visit Custom Prototypes.
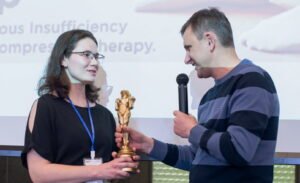
And the Rocketeer Award Goes To…
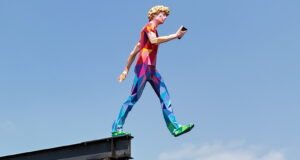
Cloudwalker
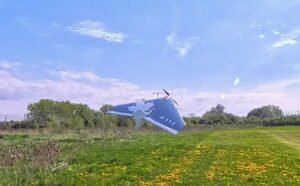
“Maplewing” – An innovative, Cost-Effective Fixed-Wing UAV
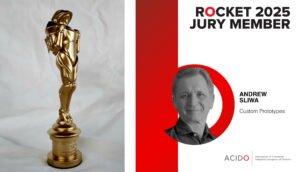